Table of Contents
You all have learned the major welding types already. Today we will discuss the types of welding joints and their applications.
Welders use the welding process in limitless ways, from simple DIY applications to the aeronautic industry.
Welding brings structures together, making stronger structures. Using correct welding joints to suit the situation is crucial; otherwise, the outcome will be disappointing.
Why are there different types of welding joints?
Different welding joints have to bear different forces. Different welding joint types have different strengths. If the welder uses the wrong welding joint, the final structure will not bear the force applied to it. It will break or distort. The results may sometimes be hazardous.
Therefore, knowing different types of welding joints and when to use them is a must to become a skilled welder. In the welding industry, there are 05 basic types of welding joints. Let us see what they are.
Basic types of welding joints
Welding joint types are easy to learn by understanding their cross-section view. The 05 basic types of welding joints are as follows;
- Butt Joint
- Corner Joint
- Lap Joint
- Edge Joint
- Tee Joint
Before going into details, do you know what a weldment is?
It is the term used to describe a set of parts or materials welded together. Basically, it is a joint where different metal parts are joined together. In other words, when a welder makes a weld joining two or more metals together, it creates a ‘weldment‘.
You will see weldments on pipes, castings, sheet metal, or on many other applications. Now, we will see what these joint types are in detail.
Butt Joint
This weld joint is comparatively the easiest and most commonly used in welding projects. Another term for butt joint is square-groove weld.
Welders use butt joint to weld two metal pieces on the same plane, side by side, parallel to each other. This is the universally accepted welding joint used when it comes to the types of welding joints in pipe welding. Butt joint use different welding styles as;
- Square-groove butt weld
- Bevel-groove butt weld
- V-groove butt weld
- J-groove butt weld
- U-groove but weld
- Flare-V- groove butt weld
- Flare-bevel-groove butt weld
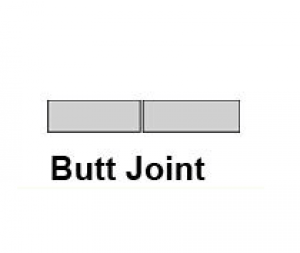
Because of the convenient positioning of the metal pieces to be weld, making a butt weld joint is very easy for a skilled welder. Two pieces are joined at the adjoining seam.
Above mentioned styles happen to depend on the material thickness and the form of the joining surface preparation. Welders use butt joints on both sides of the joint to match with the requirement or as per the wedding symbol.
Use: Joining pipes, valves, fittings, or valves.
Corner Joint
Corner joint is very popular in sheet metal welding projects. When the welder needs to join two metal pieces that come together at a 900 angle, they use Corner joint welding.
The two materials make an L at the outer edge of the metals. You can see corner joint welds in metal box and box frame construction. Welders use below mentioned welding styles when making corner joints;
- Butt-weld/ square-groove weld
- U-groove weld
- Spot weld
- V-groove weld
- Bevel-groove weld
- Fillet weld
- Flare-V-groove weld
- Corner-flange weld
- J-groove weld
- Edge weld
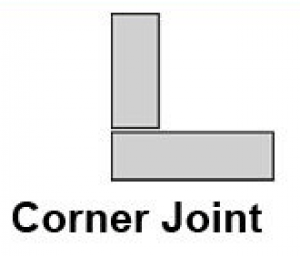
Above mentioned, different welding styles are used in different situations.
Welders use fillet weld style commonly in making corner joints where the two metal sheets are intersecting.
Corner joints come in two variations as the open corner and closed corner joint. The closed corner joint is very similar to the square-butt joint. Open corner joints have fewer defects compared to closed corner joints.
Uses: Constructing metal box edges and box frames
Lap Joint
The lap joint is the third type of welding joint we are discussing.
When the material pieces to be weld are in an overlapping position, welders make lap joint welding to attach them together.
Lap joints are a kind of fillet type weld. They make a fillet weld on the seam of the overlapping pieces. Welders make lap joints on both sides or one side of the seam as per the requirement and situation.
When two joining pieces have different thicknesses, lap joints make a strong weld. There can be one or more welding passes in a lap joint. Below are the welding styles and metal fabricators using in making this joint type:
- Fillet weld
- Spot weld
- Bevel-groove weld
- J-groove weld
- Slot weld
- Plug weld
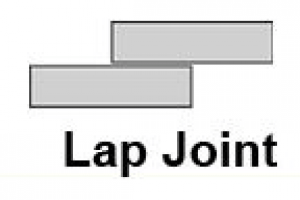
Typically a lap joint does not make an edge preparation on the edges of the joining pieces.
The welders do not usually groove the base metal before making the joint. This joint type is mostly visible in sheet metal welding.
Rarely, you will find the lap joint welds on thicker material such as pipe and plates. The possibility of corrosion is high in lap joints due to the overlapping of materials.
Use: Metal sheet welding, widely used in the laser beam, electron beam and resistance spot welding
Edge Joint
Welders use edge joints when joining sheet metals, having flanging edges.
Here, the metal pieces are brought together side by side, parallel to each other, and welding is done along the same edge. This is a groove type weld.
On some occasions, welders use filler metal to fuse and reinforce the joint. Same as other joint types, edge joints can be made on both sides or one side of the joint seam. Using below welding styles, welders make edge joints:
- Butt-weld/ square-
- groove weld
- Bevel-groove weld
- J-groove weld
- V-groove weld
- U-groove weld
- Edge-flange weld
- Corner-flange weld
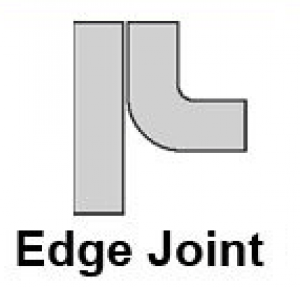
Edge joints seem to be less strong as the weld does not penetrate the thickness completely at the joint. Therefore, it is good for joints under less stress and pressure. This is a groove weld type.
Uses: Joining edges of mufflers or metal sheets with flanging edges.
Tee Joint
The last welding joint type in basic welding joint types is the Tee joint.
When the two joining materials intersect at an angle of 90° coming together, they form a T shape joint. In other words, this joint is not at an edge of a metal piece, but in the middle of a metal surface. Also, when a pipe meets a base plate, it makes a T joint.
Welders use fillet weld type when making tee joints. A usual tee joint does not require any grooving unless the base metal plate is too thick.
Welders rarely use the Submerged Arc welding method when making tee joints, as it makes some facets in the process. Below mentioned welding styles can make tee joints;
- Fillet weld
- Plug weld
- Shot weld
- Bevel-groove weld
- Flare-bevel-groove weld
- J-groove weld
- Melt-through weld
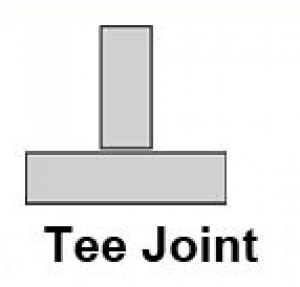
Lamellar tearing is a common defect that comes with tee joints. As tee joints experience high constraint, lamellar tearing occurs.
Welders use stoppers to prevent this joint deformation. Tee joint is also a fillet type weld and done on both sides of the welded metal piece.
Use: Joining pipes to base metals, joining metal pieces perpendicular on metal bases.
Fillet welding Joints?
Have you heard about Fillet welding joints?
It is another name that describes lap, corner, and tee joints. Fillet joints mostly use arc welding.
When constructing piping systems, joining pipes to socket joints, welders use fillet joints mostly. And, the edge preparation is not compulsory or needed in this welding joint making. Also, this welding joint preparation is less expensive than butt welds.
IMPORTANT NOTES:
- Welding variables need to be properly controlled to avoid other deformations like porosity, incomplete penetration, slag inclusion, burn through, cracking, lamellar tearing, and lack of fusion.
- Welders must use the appropriate welding methods and procedures to match with the welding joint they are making.
- Knowing all the types of welding joints symbols is crucial to get the job done properly. Otherwise, the needed strength of the welded structure will not be there in the final outcome.
- The strength of a weld joint does not solely depend on the size of the weld. The metal type, which makes the joint plays a huge part in making the joints strong.
- Surfaces and edges of the metals, making the joint must be clean without any foreign material on it to make a clean, strong, and complete weld joint.
We now know all the basic types of welding joints and their features. Let’s quickly look at the available welding positions.
Welding Positions
Types of welding joints and positions are two topics that come together.
All welding processes cannot be done for all welding positions. Some welding processes can work on all welding types, while some processes can only cater to a couple of positions.
Welders classify all welding applications depending on the position of the welded joint on the base plates, or the workpiece.
The position of the welding operator facing the welding workpiece determines these basic welding positions. The position matters a lot in welding as the flow of the molten filler material depends on gravity.
What are the basic welding positions?
Flat position
Horizontal position
Vertical position
Overhead position
Both groove welds and fillet welds are made under these four positions.
Flat position
This is the easiest position to perform welding. Down hand position is another name to call the flat position.
In this position, welders weld on the top side of the welding joint faster and easier. The molten metal flows downwards into the joint, sealing it.
Horizontal Position
Welding under this position is much more difficult than the flat position for an apprentice welder. As you get skilled, handling this position will be easy.
In groove welding under the horizontal position, you will find the weld axis along a horizontal or nearly horizontal plane. Then, the face of the weld sits almost in a vertical plane.
In fillet weld under this position, welding happens on the top of the surfaces that are almost horizontal or perpendicular to the vertical surface. Welders have to hold the torch at a 45° angle to get the job well done.
Vertical position
Both metal plates and the weld joint lie vertically in this welding position. As gravity works on the molten metal, it tends to dribble downwards piling up. To avoid this, welders use downhill or upward vertical positions.
Overhead position
In this welding, position welding happens from the underside of the welding joint. It needs a lot of skill to manage this welding position as it is much complicated and difficult.
In this position, molten metal sagging and bead making on the plate are common to see. Keeping the molten puddle small is very important to avoid this issue.
Note: Apart from these positions, there are pipe welding positions as well, which is quite a broad topic to look into.
Among the types of welding joints and symbols, numbers, and letters are assigned to identify the welding positions and type of the weld. That classification is as follows:
1 = Flat position
2 = Horizontal position
3 = Vertical position
4 = Overhead position
F = Fillet Weld
G = Groove Weld
For example, 2G means Horizontal position Groove weld. Understanding all the welding joints symbols is crucial to reading welding illustrations and drawings on the pathway to become a professional welder.
Summary
There are five basic types of welding joints, namely, Butt joint, Corner joint, Lap joint, Edge joint, and Tee joint.
Different joints have different characteristics, and welders must know when to use which.
Welding positions come as flat position, horizontal position, vertical position, and overhead position.
It is easy to weld in a flat welding position, while the overhead position needs more experience and skill.
We hope that our readers got a proper understanding of today’s topic. Welding is an interesting subject to learn and needs to be learned with all the small details. Last but not least, from DIY projects to bigger projects, make sure to use adequate safety measures before and while performing welding.
Recommended reading:
- 4 Different Types of Welding Processes & Pro tips
- Top Welding Machine Brands Ruling The World [Updated 2022]
- Top 14 Best Stick Welder for Beginner 2022 – Under $200|$500|$1000
I am preparing a presentation on welded joints to qualified welders. I would like to use your pictures, types of welding joints n the PowerPoint presentation.
I will include a connotation that the figure was supplied by BE WITH NICK on the slide.
Thanks for your blog, nice to read. Do not stop.
It’s really a nice and helpful piece of information. I’m satisfied that you shared this
useful info with us. Please keep us informed like this.
Thank you for sharing.
Im very happy to uncover this site. I wanted to thank you for ones time for this particularly wonderful read!! I definitely appreciated every bit of it and i also have you book marked to see new information in your site.
Good post. I learn something totally new and challenging. Thank you so much!!!