Welcome to our comprehensive guide on STT welding! Whether you’re new to the world of welding or an experienced professional looking to expand your skill set, this blog post will provide you with valuable insights into the art of STT welding. From its definition and advantages to its applications and techniques, we’ve got you covered.
Post Highlights:
What is STT Welding?
STT (Surface Tension Transfer) welding is an advanced welding process that ensures precise control over the weld puddle, resulting in exceptional weld quality. It utilizes a modified short-circuit transfer method, where the welding current is pulsed to maintain a controlled droplet transfer. This technique minimizes spatter, reduces heat input, and produces clean, high-quality welds.
Benefits of STT Welding:
- Superior Weld Quality: STT welding delivers welds with minimal defects, such as porosity or cracks, resulting in stronger and more reliable joints.
- Reduced Spatter: The controlled droplet transfer in STT welding significantly reduces spatter, making cleanup and post-welding operations easier.
- Lower Heat Input: Compared to traditional welding techniques, STT welding generates less heat, minimizing the risk of warping or distortion in the workpiece.
- Increased Productivity: The high deposition rates and reduced clean-up time associated with STT welding lead to improved productivity in welding operations.
Applications of STT Welding:
STT welding finds applications in various industries, including:
- Structural Fabrication: STT welding is commonly used in the construction of buildings, bridges, and other large-scale structures, ensuring strong and durable connections.
- Pipelines and Oil/Gas Industries: The high-quality welds produced by STT welding make it ideal for pipeline construction and welding in the oil and gas industry, where reliability is paramount.
- Automotive Manufacturing: STT welding is employed in the production of automobile components, such as chassis frames and exhaust systems, due to its ability to deliver high-strength welds.
- Aerospace and Defense: The aerospace and defense industries rely on STT welding for its precision and repeatability, ensuring the integrity of critical components.
The STT Process
The STT process involves a unique combination of arc and voltage control, wire feeding, and advanced waveform technology. These elements work together seamlessly to create a stable and controlled welding environment. The process begins with the arc initiating between the electrode and the base metal. Once the arc is established, a short circuit occurs, generating a high current surge that heats the wire. The heat melts the wire and creates a small drop, which is then propelled onto the base metal’s surface. This controlled droplet transfer ensures precise and consistent welds.
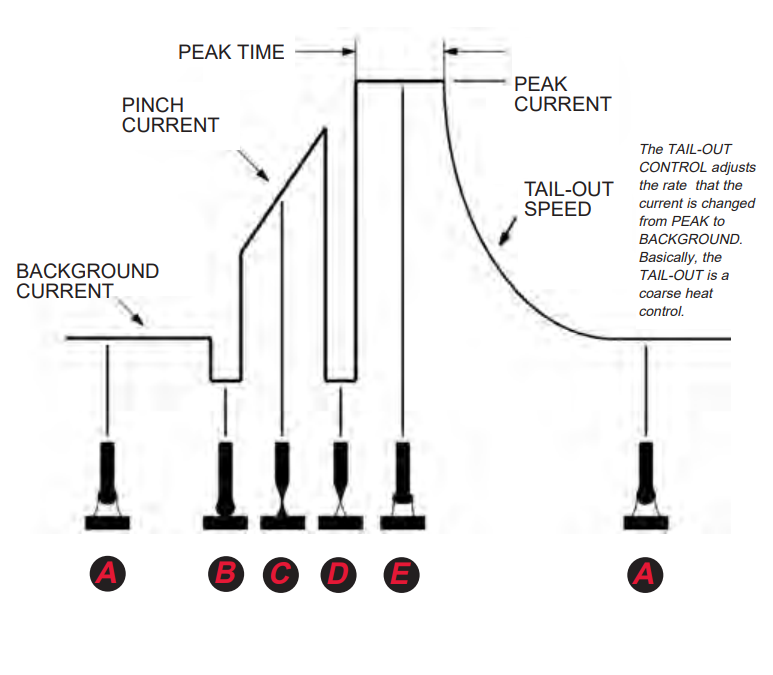
Comparing STTĀ® to GTAW/SMAW
STT welding offers several advantages over other popular techniques like GTAW (Gas Tungsten Arc Welding) and SMAW (Shielded Metal Arc Welding). While GTAW is known for its clean and high-quality welds, STT provides a similar level of precision with increased efficiency and reduced heat input. SMAW, on the other hand, often results in more spatter and requires extensive post-weld cleanup, whereas STT welding minimizes these issues, saving both time and effort.
Is STT welding suitable for thin materials?
Yes, STT welding is versatile and can be used on a wide range of material thicknesses, including thin materials. Its low heat input helps prevent burn-through or distortion.
Can STT welding be automated?
Absolutely! STT welding can be automated using robotic systems, providing consistent and accurate welds for high-volume production.
How does STT welding differ from other welding techniques?
Unlike traditional welding methods, STT welding controls the transfer of droplets, resulting in reduced spatter, lower heat input, and superior weld quality.
What does STT stand for in welding?
STT stands for Surface Tension Transfer, a welding process that offers exceptional control, stability, and reduced spatter.
How does STT welding compare to GTAW?
While GTAW produces clean welds, STT welding offers similar precision with increased efficiency and reduced heat input.
Does STT welding minimize spatter?
Yes, STT welding significantly reduces spatter, resulting in cleaner and aesthetically pleasing welds.
What industries can benefit from STT welding?
STT welding finds application in various industries, including automotive, structural steel, and pipe fabrication, where precision and high-quality welds are crucial.
Conclusion:
STT welding is a game-changer in the world of welding, offering superior weld quality, reduced spatter, and increased productivity. Its versatility and applications across various industries make it a valuable skill for welders. By mastering the art of STT welding, you can achieve stronger, more reliable welds while minimizing defects and maximizing efficiency. Embrace the future of welding with STT and unlock a world of possibilities.
Remember, practice and continuous learning are key to mastering STT welding. So, go ahead and explore this innovative welding technique to elevate your welding skills to new heights!